The 5 Whys Analysis
The 5 Whys Analysis
By: Mohammed Alqaq
The 5 Whys analysis is the ultimate root cause analysis tool that helps the CSM not only to know what the problem is but will allow dissect the problem and reveal its underlying causes quickly.
It is one of the most effective tools for root cause analysis in the Lean management practice. Every team faces roadblocks in its daily work, and using the 5 Whys analysis will help you find the root cause of any problem and protect the process from recurring mistakes and failures.
One of the key factors for the successful implementation of this technique is to make an informed decision. A decision-making process based on an insightful understanding of what is happening.
By applying the 5 Whys analysis, you want to get to the problem’s root and then find the way to fix it. 5 Whys analysis may show you that the source of the problem is quite unexpected and most often problems turn out to be human or process problems rather than technical.
Finding and eliminating the root cause is crucial if you want to avoid iteration of failures. Therefore, the 5 Whys analysis aims to inspect a certain problem in depth until it shows you the real cause.
Make sure to ask “Why” as many times as you need to complete the process and take appropriate actions, the “5” here is just a number.
When to Use a 5 Whys Analysis
You can use 5 Whys for troubleshooting, quality improvement, and problem-solving, but it is most effective when used to resolve simple or moderately difficult problems.
The 5 Whys analysis can often direct you quickly to the root cause of a problem. So, whenever a system or process isn’t working properly, give it a try before you embark on a more in-depth approach – and certainly before you start thinking of solution development.
By repeating “WHY” five times, the nature of the problem and its solution becomes clear.
The Benefits of 5 Whys Analysis
The main benefit of the Five Whys is that it is one of the most powerful assessment methods of all non-statistical analyses. It can uncover and trace back to problems that were not very clear or obvious.
- Helps identify the root cause of a problem
- Understand how one process can cause a chain of problems
- Determine the relationship between different root causes
- Effective without complicated evaluation techniques
How to use the 5 Whys
The 5 Whys approach is not a solo-based activity, it is a teamwork. You need to gather a team from different departments who are familiar with the process to be investigated. By having a cross-functional team, you will receive many unique points of view. With this, you will collect enough information to make an informed decision.
Work with the team to define the problem statement. This will help you to characterize the scope of the issue you investigate.
Start the process by asking “why the problem is happening?“. You need to find answers that are based on facts, not just theories. You need to look for the records of what has happened, not guesses.
You can go deep and ask Why as many times as needed using the previous answer to base your question on until you figure out the root cause of the initial problem.
At the time when you no longer receive good responses, you need to stop asking and if you haven’t reached to the root cause of the problem, you might need to consider a more in-depth analysis.
If you’ve found more than one cause, repeat the 5 Whys analysis for each cause until you find a single root cause for each one. It is also important to ensure you haven’t stopped too soon and take it to the point where the team provides no reasonable responses.
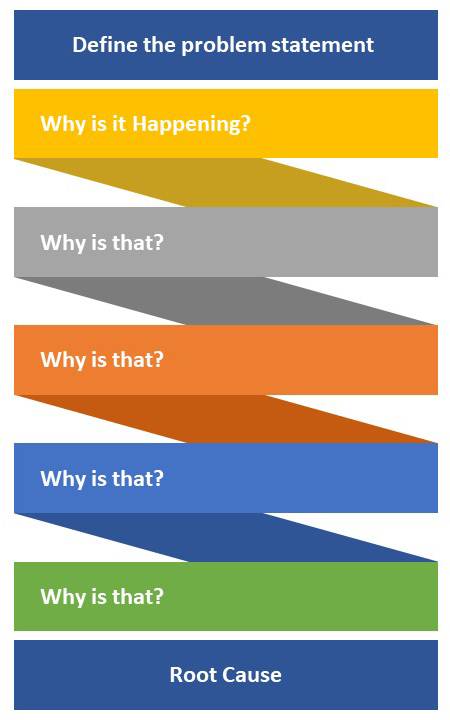
Root Cause Corrective Actions
Once you identify the root cause of the problem, the team should discuss a list of corrective actions or countermeasures to prevent the problem from recurring. The 5 Whys Master should then assign which team members should take responsibility for each item on the list.
It’s important to monitor how successful your countermeasures are in stopping the problem. If they aren’t as effective as you need them to be, means you haven’t found the true root cause, and you need to repeat the 5 Whys analysis again.
Record your findings and distribute them throughout your organization so that everyone can learn from this particular case study.
Techniques Used in 5 Whys Analysis
- The Fishbone Diagram: Causal diagrams created by Kaoru Ishikawa that demonstrate the potential causes of a particular event
- A Tabular Format: It refers to data that is organized typically in rows and columns or possibly in a more complicated structure.
The 5 Whys History
The technique was originally developed by Sakichi Toyoda, the Japanese industrialist, inventor, and founder of Toyota Industries in the 1930s and it became popular in the 1970s. It was used within the Toyota Motor Corporation during the evolution of its manufacturing methodologies.
The architect of the Toyota Production System, Taiichi Ohno, described the five whys method as “the basis of Toyota’s scientific approach by repeating why five times the nature of the problem, as well as its solution, becomes clear. “The tool has seen widespread use beyond Toyota and is now used within Kaizen, lean manufacturing, lean construction, and Six Sigma.
It is simple, and it works.